Supercharge your Engineering Team With Modern Engineered Labor Standard Tools
Warehouses have hundreds, if not thousands, of processes and tasks. Engineered Labor Standards are critical for increasing performance but can be costly if focused on the wrong processes. Takt enables engineering and continuous improvement teams with the tools they need to build and maintain better-engineered labor standards.
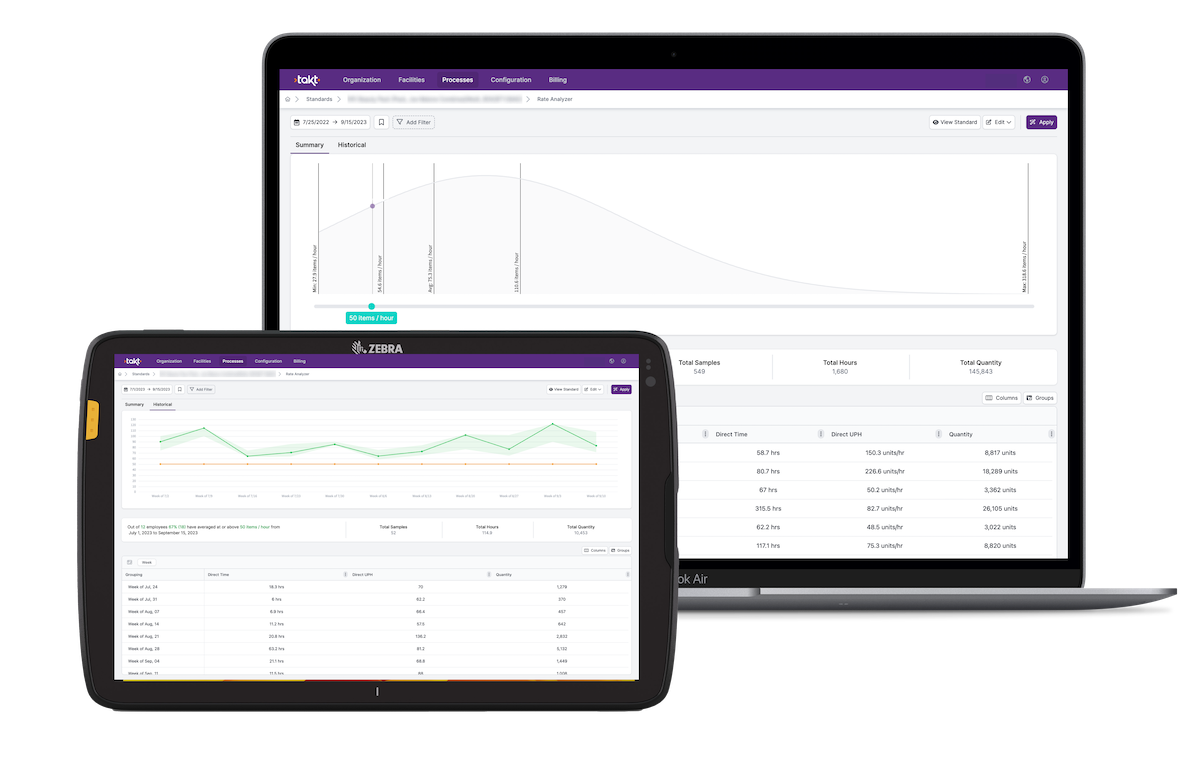
Single-Metric Standards
Define units per hour (UPH), weight per hour (WPH), or volume per hour (VPH) based standards.
Multi-Metric Standards
For more complex processes, create multi-metric standards based on quantity, weight, volume, and travel time.
Real-Time Monitoring
Monitor your processes and standards in real-time, so that continuous improvement teams can easily prioritize.
Evolve Rates Over Time
Rates should be continuously evaluated and evolved over time to account for seasons or increasing expectations.
Manage Labor Standards Across the Network
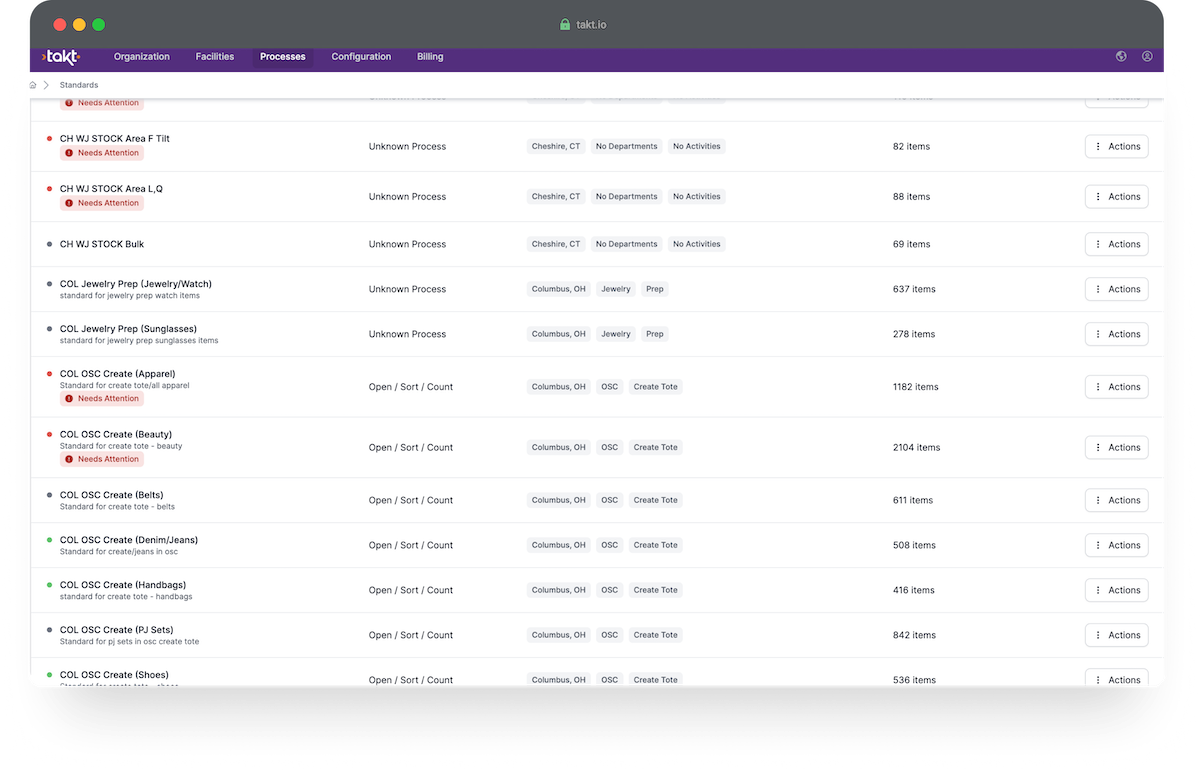
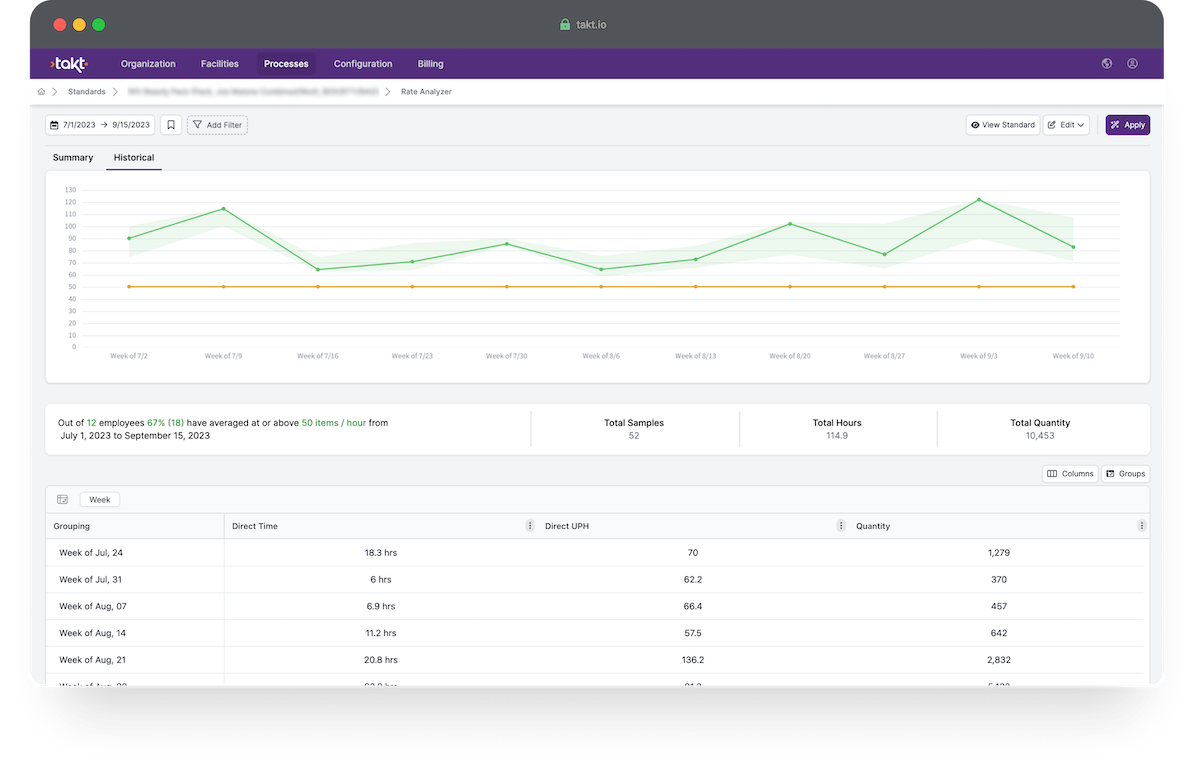
Evaluate Engineered Labor Standards
Engineers and operators need to periodically check to ensure labor standards are accurate and correct by benchmarking recent performance against the engineered labor standard. Easily compare actual facility performance against the standard with performance distributions, analyze trends, and identify process bottlenecks that may be impacting the facility.Standards Based Coaching
Leverage engineered labor standards to measure employee or team labor productivity. Identify opportunities for improvement and trigger observations. Supervisors can use productivity metrics and their observations to provide specific feedback on an employee or teams process, set realistic goals based on facility performance, and track progress towards the goal.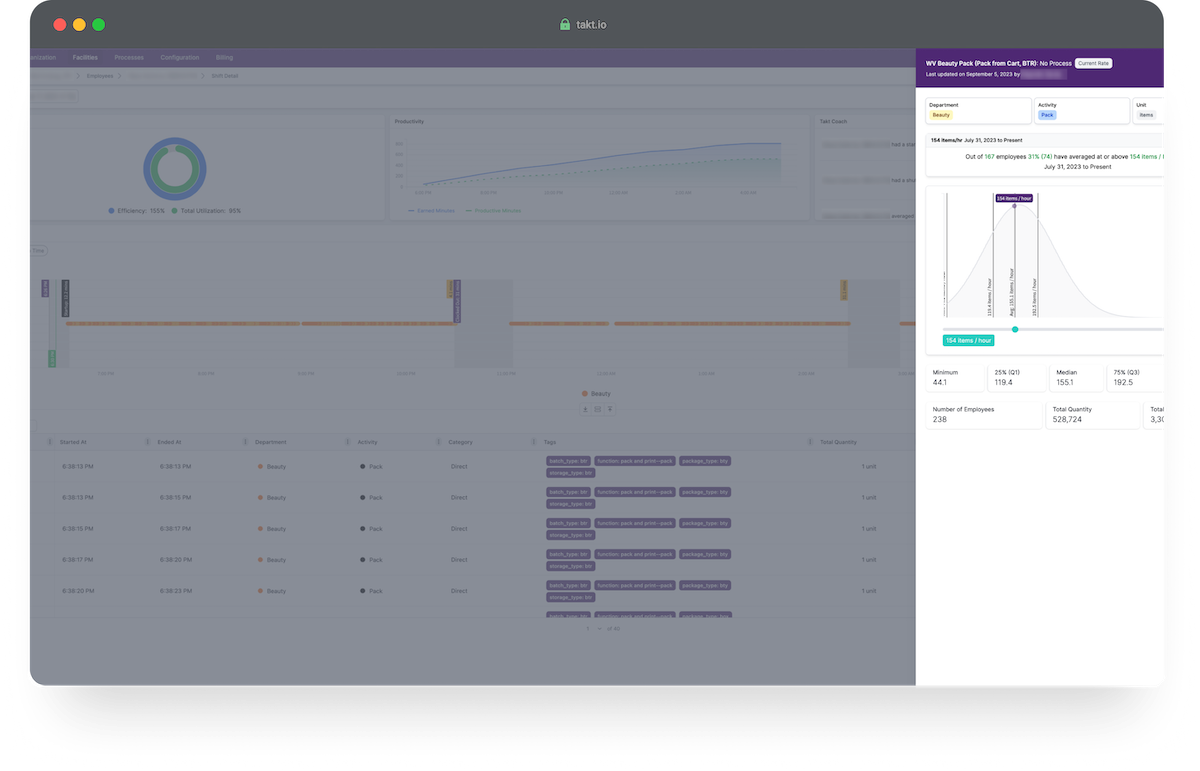
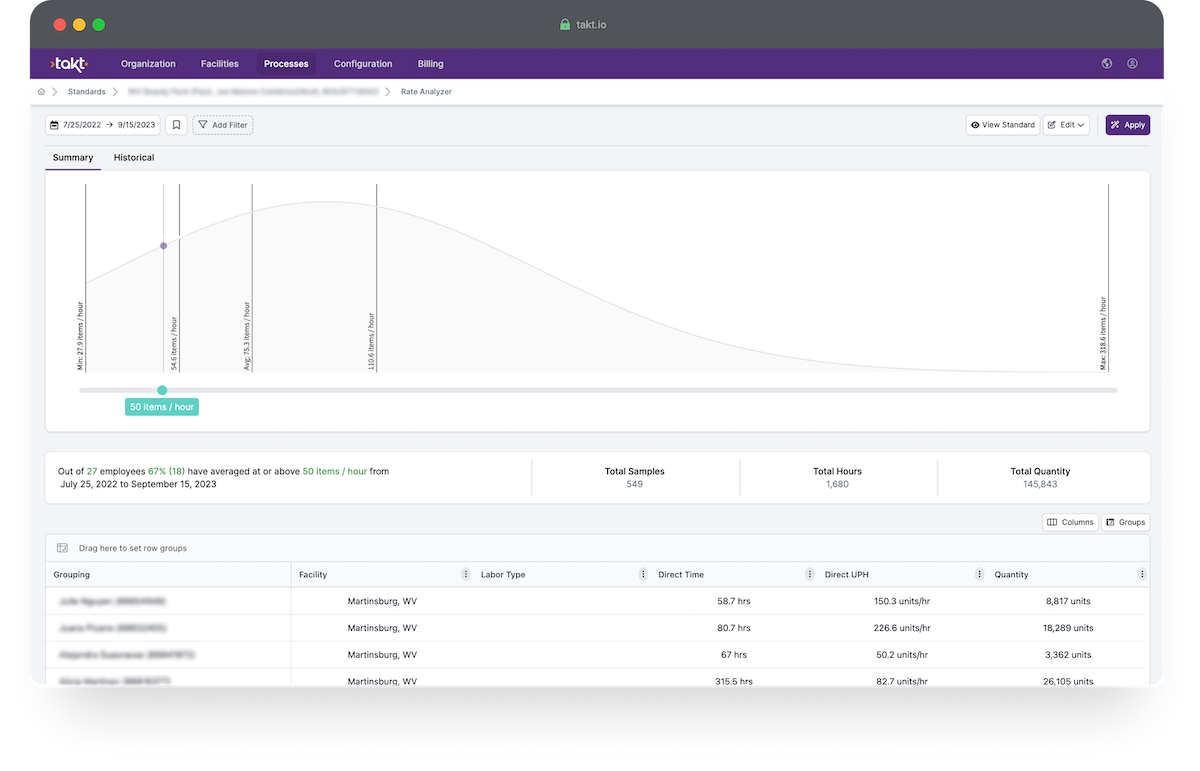
Develop Labor Baselines
In today's market warehouses don't always have time or budget to develop engineered labor standards. Takt can help operations develop labor baselines using historical performance. Takt develops a distribution of performance and recommends a rate based on engineering best practices to help increase warehouse productivity.
Common Labor Standards Questions
What are engineered labor standards?
Warehouse engineered labor standards (ELS) are the amount of time that it should take a qualified employee to complete a specific task, working at a normal pace, under qualified supervision, and experiencing normal fatigue and delays. ELS are developed using time and motion studies, and they take into account all of the factors that can affect the time it takes to complete a task, such as the distance traveled, the weight of the items being handled, and the complexity of the task.
ELS are used for a variety of purposes in warehouses, including:
- Setting staffing levels. ELS can be used to determine how many employees are needed to complete a specific task or set of tasks. This information can then be used to develop staffing schedules and to ensure that there are enough employees to meet the demands of the business.
- Measuring productivity. ELS can be used to measure the productivity of individual employees and teams. This information can then be used to identify areas where improvement is needed and to track progress over time.
- Improving efficiency. ELS can be used to identify and eliminate bottlenecks and inefficiencies in warehouse operations. For example, if the data shows that employees are spending a lot of time traveling between different areas of the warehouse, the engineer can look for ways to reduce the travel time.
Here are some examples of warehouse engineered labor standards:
- Time to pick an order
- Time to pack an order
- Time to load a truck
- Time to unload a truck
- Time to put away a pallet
- Time to retrieve a pallet
- Time to travel between different areas of the warehouse
How do you develop engineered labor standards?
There are a number of methods that can be used to develop warehouse engineered labor standards. The most common methods are:
- Time and motion studies. Time and motion studies involve observing and timing employees as they perform their jobs. The data collected from time and motion studies can then be used to develop ELS.
- Predetermined motion time systems (PMTS). PMTS are databases of predetermined time values for basic body motions, such as reach, move, turn, and grasp. PMTS can be used to develop ELS for complex tasks by combining the time values for the individual motions that make up the task.
- Work sampling. Work sampling is a statistical technique that can be used to estimate the amount of time that employees spend on different activities. Work sampling can be used to develop ELS by collecting data on the activities that employees are performing and then using that data to estimate the amount of time that they spend on each activity.
The best method for developing warehouse engineered labor standards will vary depending on the specific needs of the warehouse. For example, if the warehouse has a lot of repetitive tasks, time and motion studies may be the best method. If the warehouse has a lot of complex tasks, PMTS may be the best method. And if the warehouse has a limited budget, work sampling may be the best method.
Once the ELS have been developed, they should be reviewed and updated on a regular basis to ensure that they are accurate and up-to-date. The ELS should also be reviewed and updated whenever there is a significant change in the warehouse operations, such as a new process being implemented or a new piece of equipment being installed.
What are the benefits of engineered labor standards?
- Improved efficiency and productivity: Engineered labor standards can help to identify and eliminate bottlenecks and inefficiencies in warehouse operations. This can lead to significant improvements in efficiency and productivity.
- Reduced costs: Engineered labor standards can help to reduce labor costs by ensuring that the right number of employees are staffed for each task. They can also help to reduce the amount of overtime that is needed.
- Improved customer service: Engineered labor standards can help to improve customer service by ensuring that orders are picked and shipped on time and accurately.
- Increased throughput: Engineered labor standards can help to increase throughput by ensuring that the right number of employees are staffed for each task and that they are working at an efficient pace.
Does a Labor Management System (LMS) help me manage engineered labor standards?
A labor management system (LMS) can help you manage engineered labor standards in a number of ways, including:
- Tracking actual performance. LMS systems can track the actual time it takes employees to complete different tasks. This information can then be compared to the engineered labor standards to identify areas where improvement is needed.
- Identifying bottlenecks and inefficiencies. LMS systems can also be used to identify bottlenecks and inefficiencies in warehouse operations. This information can then be used to improve the overall efficiency of the warehouse.
- Setting staffing levels. LMS systems can be used to set staffing levels based on the engineered labor standards and the expected workload. This helps to ensure that there are enough employees to meet the demands of the business without overstaffing.
- Providing real-time feedback to employees. LMS systems can provide real-time feedback to employees on their performance compared to the engineered labor standards. This feedback can help employees to improve their performance and to identify areas where they need additional training.
- Generating reports. LMS systems can generate reports on employee performance, staffing levels, and other metrics related to engineered labor standards. These reports can be used to track progress over time and to identify areas where further improvement is needed.
What is the Methods-Time Measurement (MTM) method?
The methods-time measurement (MTM) method is a predetermined motion time system (PMTS) that can be used to develop engineered labor standards. MTM is based on the idea that all manual tasks can be broken down into basic motions, such as reach, move, turn, grasp, position, and release. Each basic motion has a predetermined time value that has been established through extensive research.
To develop an engineered labor standard using MTM, the task is first broken down into its basic motions. The time value for each basic motion is then determined using the MTM data tables. The time values for all of the basic motions are then added together to determine the overall time value for the task.
What is the Maynard Operation Sequence Technique (MOST) metod?
The Maynard Operation Sequence Technique (MOST) is a predetermined motion time system (PMTS) that can be used to develop engineered labor standards. MOST is based on the idea that all manual tasks can be broken down into basic body motions, such as reach, move, turn, grasp, position, and release. Each basic body motion has a predetermined time value that has been established through extensive research.
To develop an engineered labor standard using MOST, the task is first broken down into its basic body motions. The time value for each basic body motion is then determined using the MOST data tables. The time values for all of the basic body motions are then added together to determine the overall time value for the task.